Start » WJC Components
WJC Components
A Perndorfer waterjet cutting machine can be upgraded with numerous equipment options so that your system can do what you need it to do.
WJC Components Suitable for WJCRW
WJC Components Suitable for WJC Tube
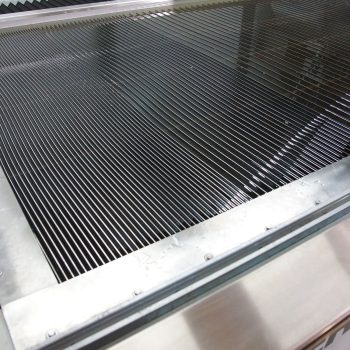
Support grate with zero stop
Depending on the system (waterjet cutting unit with pure water or abrasive) the support grate can have different designs. In the case of abrasive waterjet cutting machines usually a strip grate is used. Unlike other grate models the strips stand up the longest to the abrasive waterjet and can be placed at different distances.
The zero stop along the entire x/y axis makes it possible to arrange the raw material on the zero stop quickly and guarantees exact cuts on external contours that are already cut out.
In the case of pure waterjet cutting units a grate with a grid or a honeycomb grate made of aluminium or stainless steel is used instead of the strip grate. This is a better surface to place soft and flexible materials.
Upon request we will manufacture grates to meet customer specifications.
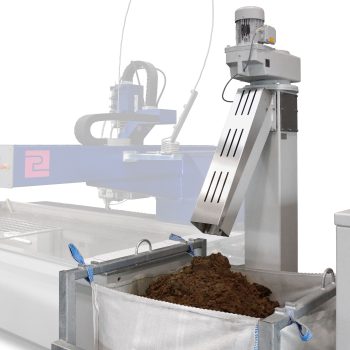
Sludge removal
The sludge removal using a screw conveyor is a Perndorfer innovation that automatically moves the sludge deposited into the cutting basin to a mobile container located outside of the unit. The sludge is just moist and does not require lots of time and effort to dry. There is no need to spend lots of time removing the cutting sludge by hand. Low maintenance, minimal energy usage, and a service life of more than 20,000 hours of operation are other advantages of Perndorfer’s sludge removal system.
Abrasive metering/abrasive system
The dosing of the abrasive is done by a method Perndorfer developed that uses a conveyor belt. This ensures exact dosing and a continual cutting process. Moreover, the amount of abrasive can be controlled during the cutting process.
A clog or the absence of the abrasive is detected reliably and evaluated. The container above the abrasive dosing part is made of plexiglass making it possible to see things at a glance
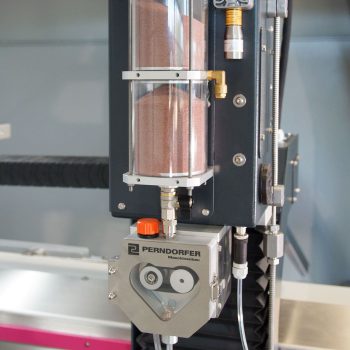
Diagonal cut compensation / ± 60° Bevel cutting head
This cutting head technology is a Perndorfer development that includes an integrated measuring system for the utmost precision.
A special algorithm analyses the contours and ensures exact square cuts.
The cutting head can function as both a diagonal cut compensation as well as a bevel head cut and allows bevel cuts of up to 60°.
Even after minor collisions the head does not have to undergo big readjustments – usually a short reference run suffices.
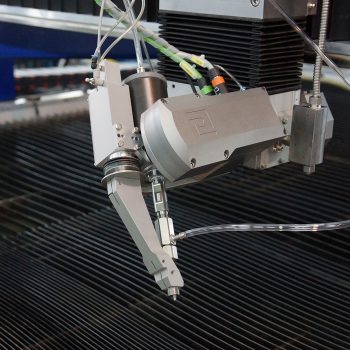
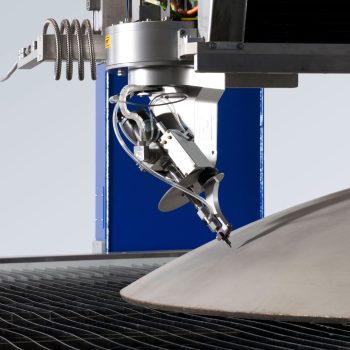
3D cutting head
The 3D cutting head ensures an even cutting quality even with complicated contours. With the b axis cuts up to ± 130° are possible. The endlessly rotating c axis has all the advantages of the integrated abrasive technology.
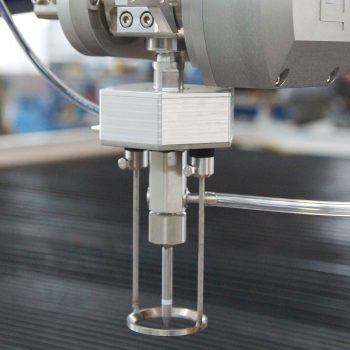
2D height sensor
The height sensor can also be used if there is a small angle or when working on the diagonal compensation.
The 2D height sensor ensures an even distance between the tip of the focusing tube and the surface of the material along the whole working area. At the same time, the height sensor reacts to any obstacles in the cutting direction and can prevent a collision.
3D height sensor
The 3D height sensor makes it possible to reliably sense the material’s surface with an inclined cutting head.
This ensures that the distance between the nozzle and the material remains the same, thus allowing for high quality bevel cuts. The 3D height sensor can also be used for straight cuts and flat material.
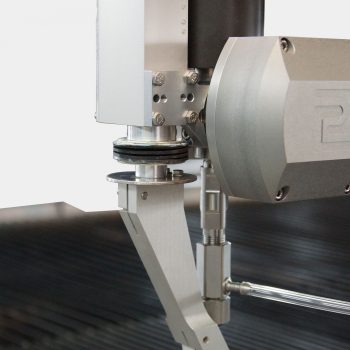
Positioning laser
With the help of a laser pointer mounted on the z axis, the desired starting point can be found easily and quickly and assumed.
Another software feature allows the laser pointer to go up and down the cutting contour. If space is limited, it is possible to do a quick visual check of the alignment of the contour on the raw material.
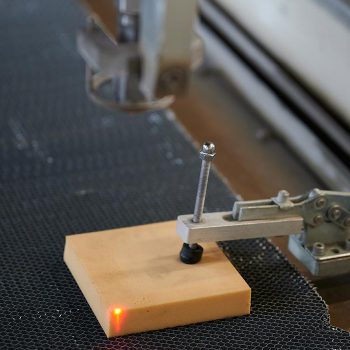
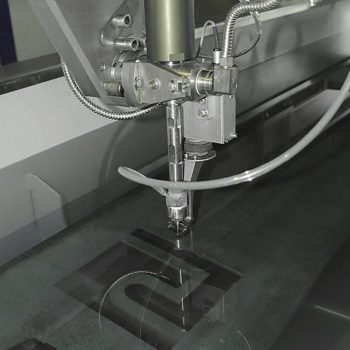
Water level regulator
Cutting under water has key advantages: There is little noise and dirt pollution. The residual energy of the waterjet dissipates and cannot do any harm.
Being able to quickly raise or lower the water level is another plus and helps save time.
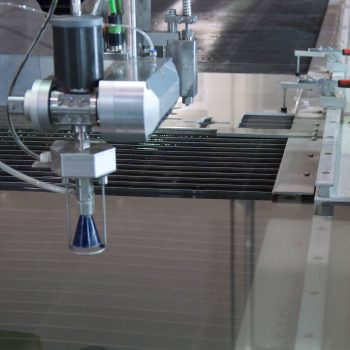
Lift tables
Lifting tables have the advantage that one zone can be cut under water while the other zone can be set up above water at the same time. The lifting tables can be coupled via the control without any mechanical effort, so that the operator has the entire cutting area of both tables at his disposal. The control raises and lowers the lifting tables quickly and fully automatically. If no zoning is required, but cutting is still to be carried out under water, a water level control is used. Here the control raises and lowers the water level quickly and fully automatic and retulates it while cutting.
To cut tubes under water a robust clamping chuck is needed that is designed for the harsh environment of the abrasive and water mixture.
Perndorfer’s clamping chuck was developed with exactly this application in mind. The clamping claws cannot get stuck and even after years they run smoothly because the mechanism is situated inside the water-tight chuck. Even machines from other companies can also be retrofitted with Perndorfer’s clamping chuck.
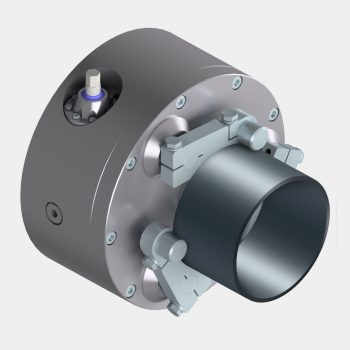
Materials like glass fibre-reinforced plastic or various sandwich materials can delaminate when pierced by the waterjet. To prevent this, an initial bore hole is made with the drilling unit. This way the waterjet can penetrate the material unhindered, and the cutting process can start.
We only use electric drilling spindles which compared to pneumatic machines use much less energy and are much more efficient.
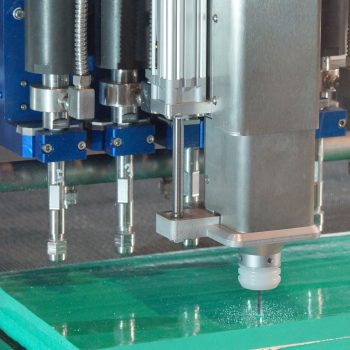
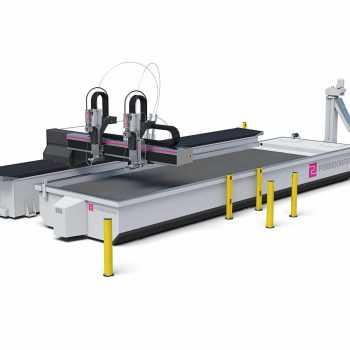
Zones are usually found in machines with larger cutting tables. The safety equipment and the machine are secured in that the setup happens in one zone while at the same time cutting takes place in another. The zones can also be activated together at the same time, and the entire cutting area is available.
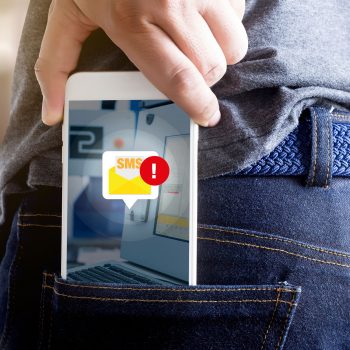
The text message notification is a useful feature for unmanned cutting. If the cutting programme aborts or is completed, the operator receives a text message.
The dimensions of the lean cutting head make closer spacing possible.
Material is better utilised in the case of small parts. Thanks to higher pressure cycles the cutting heads react especially fast.
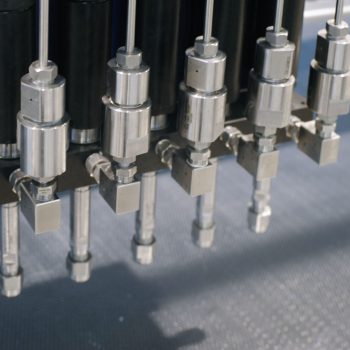
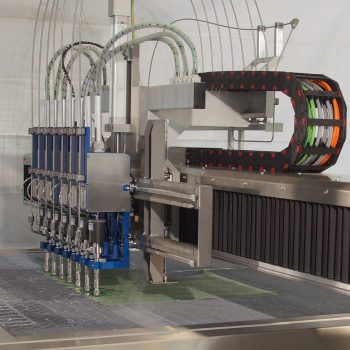
Convenient, time- and cost-saving.
The distances between the heads are usually determined by the cutting job or the nesting; the machine automatically places the cutting heads at the correct distance.
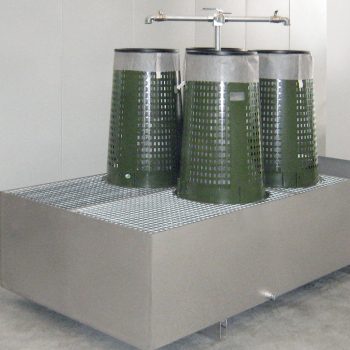
When cutting rubber, the wastewater becomes heavily polluted with particles.
Because every plastic reacts differently in water, Perndorfer is conducting tests to achieve bespoke disposal solutions right up to water recycling for recirculating the wastewater.
This is specially developed to keep splashing water and steam to a minimum.
WJC with pure water can be equipped with a catcher instead of a cutting basin. Depending on the model, the system is powered together with the gantry or by its own powertrain. In the case of shuttle tables, the catcher automatically adjusts to the height of the table.
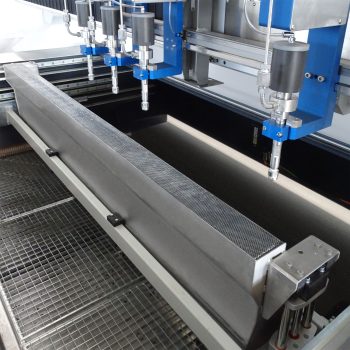
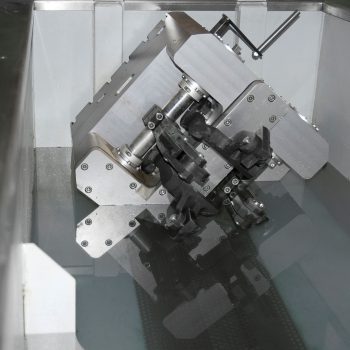
A Perndorfer innovation
The variable clamping head enables the clamping of tubes, formed tubes, and various profiles (e.g. I-sections) without any time-consuming retooling. As a result, work is guaranteed to be faster and more efficient.
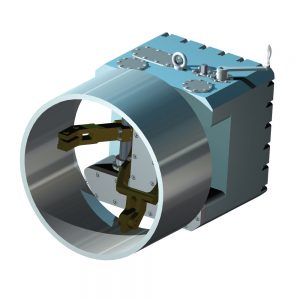
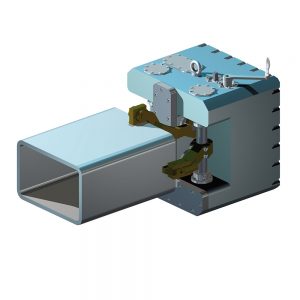
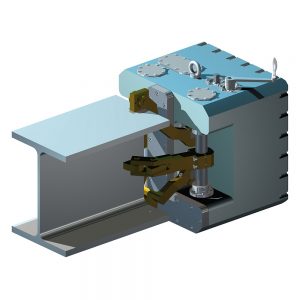
Clamping a tube, a formed tube, or an I-section.
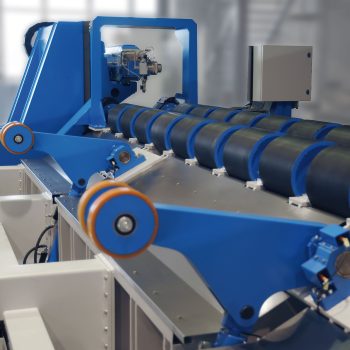
Safe and convenient feeding of the system
There is the option to fit the system with a printer (inkjet) to automatically label the tubes.
This not only labels tubes, but also accurately applies index or grade markings.
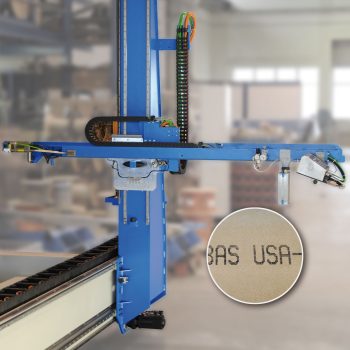
The automatically adjustable tube support (w axis) makes it possible to cut several tube segments without losing time for re-clamping.
The segments that have already been cut remain in the catcher or can be pushed back with the w axis to avoid colliding with newly cut segments.
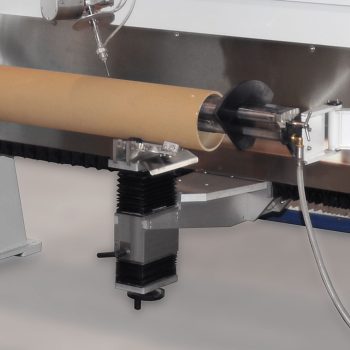
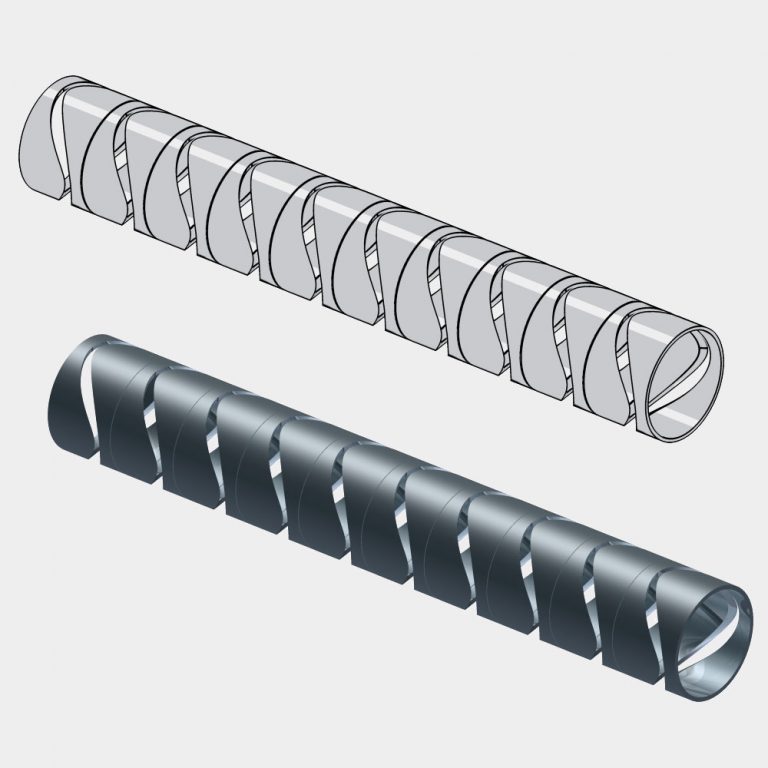
The tube cutting machine works precisely and efficiently and ensures the greatest possible yield. It is also suitable for bespoke and standardised series production of tube segments.
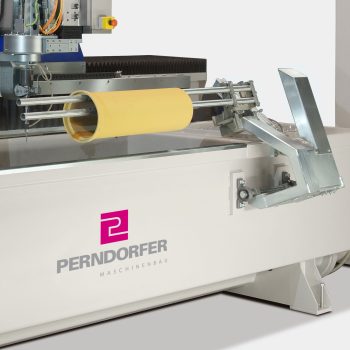
This makes it easy to conveniently load outside of the cutting basin.